
The individual construction areas
The mechanical assembly included the quette, the sheet straightener, the cooling beds 1 and 2 and the connecting roller conveyors. The upper and lower parts of the quette were pre-assembled and placed on a frame. More than 60 tonnes were moved per lift.
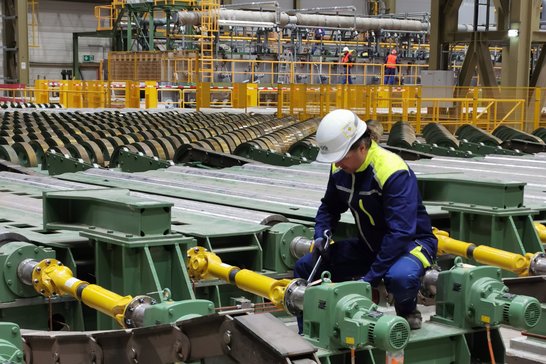
Highest precision measurement
Precise measurement technology is necessary for every successful construction site project, this project included. The individual disc rollers for the cooling beds with a weight of 4 tonnes were precisely measured with a 3D laser tracker. The height deviations are in the tenth of a millimetre range. Our experienced measurement technicians guaranteed the highest accuracy and assembly quality. Learn more about our industrial measuring here.
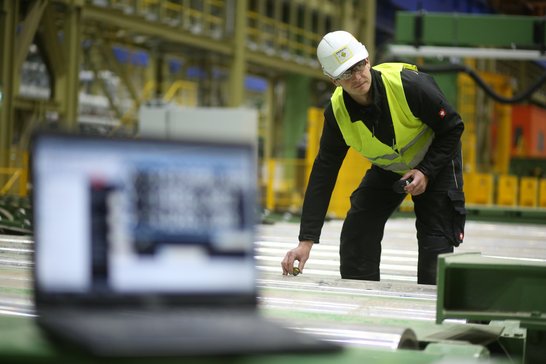
The new heat treatment line
With the new heat treatment line, more than 200,000 tonnes of heavy plate are annealed annually and then further processed. The new line is designed for plates with thicknesses of between 5 and 175 millimetres, and widths of between 600 and 3,500 millimetres. The plates have a maximum weight of 28 tonnes and lengths of between 4 and 24 metres.
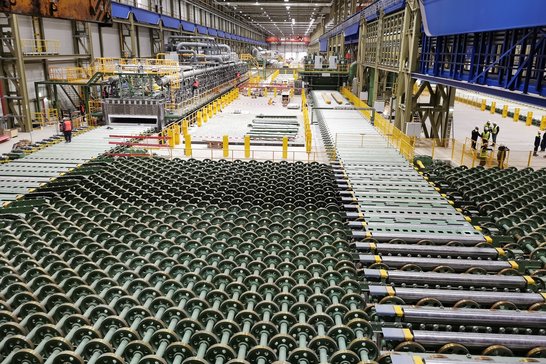
On-time and reliable
The start date for our SGS team was during the first Corona lockdown in mid-April 2020. The first plate went through the quette in early December 2020. Despite all the unexpected restrictions and the additional safety measures, our project team and installation team succeeded in completing the project on time and safely. This shows once again how quickly, flexibly and competently our employees react to unforeseen circumstances. You can rely on us even in difficult times!
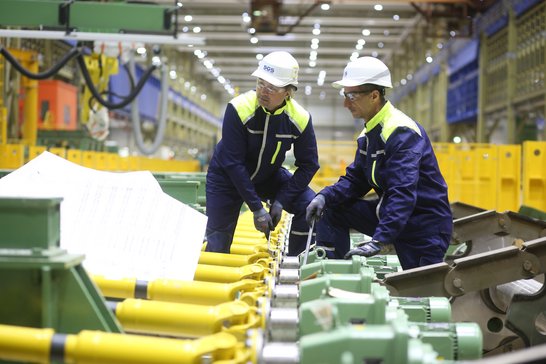
Project data
- Commissioner
- SMS group
- Customer
- Ilsenburger Grobbleche GmbH
- Industry
- Metallurgy
- Construction location
- Ilsenburg, Germany
- Contruction period
- 8 months, April 2020 – November 2020
- Contributors
- 80
- Scope of delivery & service
-
Mechanical assembly of a new heat treatment line